Buying a brand new yacht ought to be one of the best experiences of a lifetime. However, the reality is different for a small number of owners. So how can prospective boat buyers avoid unforeseen problems?
Couldn’t it be wonderful to believe that the experience of buying a new yacht is never problematic? But as with anything and everything – from cars to new homes – problems with new yachts are by no means unheard of.
Stories of keels falling off, bulkheads buckling, bond failure of structural components and so on have all had significant exposure on social media and YouTube. But how much truth is there to them? What are boatbuilders doing to address the problems? And how can buyers best protect themselves?
Fortunately the issues new boat buyers are most likely to encounter fall into the ubiquitous category of snagging a (albeit potentially long) list of relatively minor issues. Almost no new boat is without them, which is partly a reflection of the marine industry’s small scale production compared to sectors such as automotive. Yachts are still largely built and assembled by hand, which inevitably means there’s potential for error to creep into production processes, which makes effective quality control procedures essential.
Snagging timescale
Snagging procedures vary considerably between different yards, although in many cases it falls to the dealer, which can result in a range of different outcomes even for the same model of boat.
Outremer, for instance, has sold directly to clients for the past few years and has a well-defined process and timescale for dealing with problems. This starts with a week-long handover at the shipyard, where owners work with the after sales and quality control teams, as well as having the benefit of hands-on training sessions with the yard’s professional skippers.
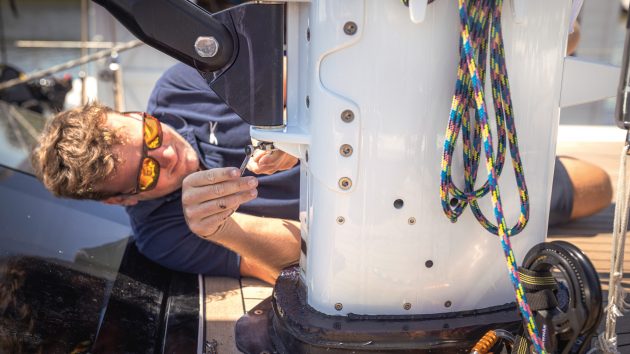
Rigging and thorough testing during Oyster’s commissioning process. Photo: Christopher Ison/Oyster Yachts
“Quality and client satisfaction are paramount for us and we’re in constant discussions with our customers and owners,” marketing director Céline Macharez told me.
After the handover process has been completed owners sail away for anything between three weeks and two months. “Then they come back to the shipyard where we check everything again and fix anything they discovered,” Macharez adds. “We know that they are engaged on bluewater cruising journeys, so even when they leave the shipyard it’s not the end of the story. Anywhere they are on the globe, they have someone to talk to and to fix their problems if they have one.”
Equally, other high-end brands including Oyster and Nautor Swan have multiple service and maintenance bases with their own staff, so any support for new owners can be provided in-house.
Article continues below…
Why do keel failures happen and what can we do to prevent it?
Matthew Sheahan investigates the incidence of keel failure in recent years and finds some worrying reports of near-misses
Second hand boats: how to buy a ready to sail yacht
It’s no secret that if you want to buy a new yacht the wait is now likely to be two…
However, this type of service can be a problem for smaller or less well established businesses. British yard Discovery Yachts, for instance, was forced into administration at the end of 2019 following a well publicised court case in which the owner of a two-year-old 58ft yacht won compensation totalling some £1.6 million.
The judge in that case wrote: “The yacht appears to have been delivered hurriedly and before it was ready to be delivered. It was delivered without an adequate sea trial or commissioning.” Some repairs were carried out after the boat crossed the Atlantic, but these were unsuccessful and it was subsequently shipped back to the UK. The judge also ruled the owner “…did not have the enjoyment and pleasure which he had justifiably expected.”
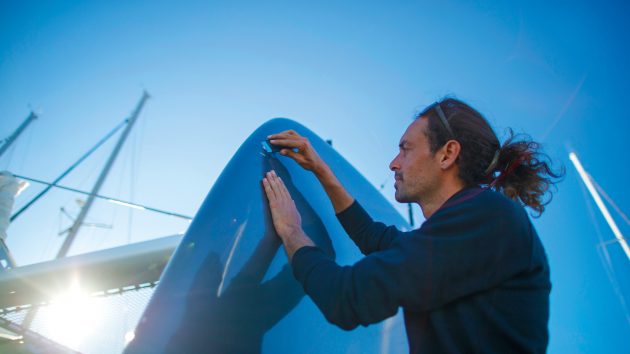
Part of the commissioning, snagging and trial sailing process at Outremer. Photo: Robin Christol/Outremer
Lloyds certification
Sadly there are other instances in which problems go beyond the mundane and easily remedied. The best known of these is possibly the Oyster 825 Polina Star lll, whose keel fell off in 2015 due to moulding defects, resulting in the yacht sinking. That incident was a factor in the company calling in the receivers due to cashflow issues three years later.
New owner Richard Hadida quickly instituted radical changes to ensure his firm has a tight grip on quality control. Under previous ownerships Oyster had in some senses been primarily a marketing operation – albeit a very successful one – with production largely subcontracted out to third party firms. It was one of these that was ultimately at fault in the Polina Star case. Hadida acted quickly to either buy the subcontractors outright, or invest in new production facilities directly owned and controlled by Oyster. Today Oysters are delivered with Lloyds Register and DNV certification.
Contest Yachts in the Netherlands also offers an example of top-notch practice, having delivered all its boats with a Lloyd’s Register Hull Construction Certificate for more than 50 years. This requires plans and structural engineering calculations to be scrutinised and approved before construction commences, followed by inspections during the build to ensure every vessel is delivered in accordance with those plans. It’s a more expensive way to build yachts than the standard industry practices required by legislation, but can give lots of reassurance.
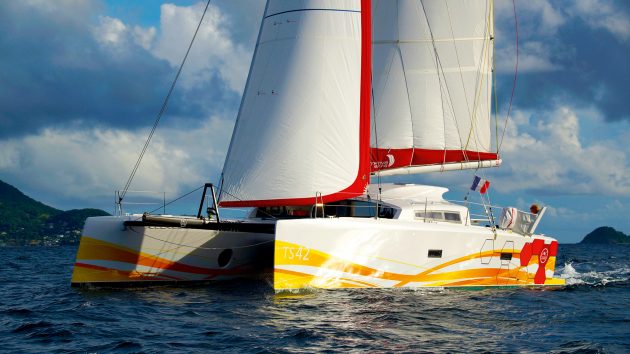
John Lawson had a TS42 catamaran that lost a keel. Analysis of hull sections found that resin infusion had failed. Photo: Courtesy of John Lawson
Quality control
Instructing a surveyor to check each construction stage while a boat is in build might sound like an ideal solution for anyone buying a new yacht, but in reality is not practical in most production yacht building environments. Nevertheless, a couple of yards are bucking the trend in this respect.
One of these is Neel Trimarans, a company that in the past has attracted online attention from disgruntled customers complaining of issues from faulty freshwater systems to deck leaks, as well as a handful of cases alleging much bigger problems. Last year the company changed ownership, who brought in new management with a brief to tackle quality control head on.
Chief commercial officer Brieuc Maisonneuve told me: “Since the change of ownership, there have been significant improvements in production processes and quality control procedures. Specifically, Neel has implemented a three stage quality check on the production line, plus a final quality control with sea trial before delivery to the dealer.
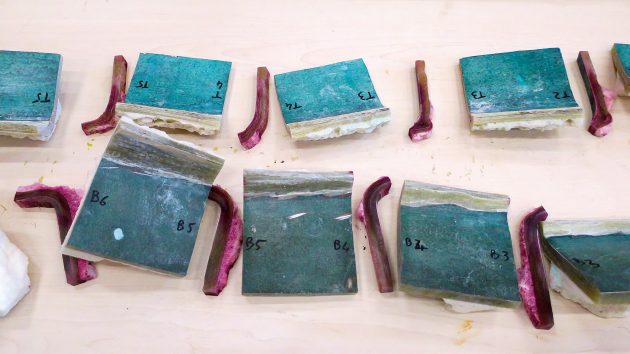
Hull section a analysis of John Lawson’s TS42. Photo: John Lawson
“We are also involving dealers more (Neel sells 95% of our production via our dealer network) in the commissioning of the boat before and after the arrival of the clients. These changes aim to address past issues and ensure that customers receive high-quality yachts that meet regulatory standards and exceed expectations.”
Righting wrongs
At the former Marsaudon Composites site in Lorient, France, where ORC catamarans are built, and a new production line for Outremer 45s has recently been established, a specialist NDT (non destructive testing) surveyor has been engaged to visit three times a month to monitor the progress of boats in build. These surveyors more usually work with IMOCA 60s and Class 40s.
This follows a legal case in the Tribunal de Commerce de Lorient that Marsaudon Composites lost and subsequently led to it becoming insolvent in September 2023. The case was brought by John Lawson, who bought a new TS42 (a model now renamed ORC42) in 2016, but encountered numerous problems within his first two years of ownership, including dry areas of laminate and the loss of a keel during an Atlantic crossing.
It’s important to note the latter isn’t the catastrophic failure it would be on a monohull, since it’s not a ballast keel and the hull retained watertight integrity. Nevertheless it’s not the kind of problem anyone expects to encounter with a new yacht.
Among other things, the expert appointed by the Tribunal found the keels had design and build faults that led to the breakage, the hull mouldings had areas in which the resin infusion process failed, rudders were badly built, and a strengthener in each hull was unsafe.
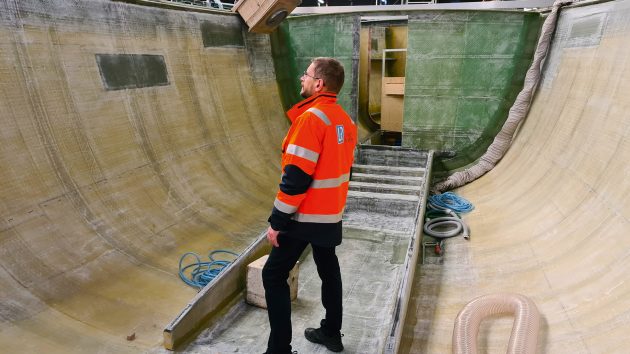
Quality control during build should reduce problems later on. Here a Lloyd’s inspector visits a Contest hull. Photo: Contest Yachts
Once it became clear that matters had stalled after the judgement, with his boat still in the hands of Marsaudon Composites’ receiver, Lawson posted a video on YouTube, which quickly went viral with more than 140,000 views. His status as winner of a legal case – albeit after considerable costs and a five-year wait – clearly helped his video stand out from others that lack third party professional expertise to collaborate the allegations.
The Grand Large Yachting group, which includes Outremer, Gunboat, Garcia, Allures and RM Yachts, bought certain assets of Marsaudon Composites from the receiver last autumn, including some intellectual property and tooling of ORC Catamarans, but without responsibility for various liabilities, including those relating to Lawson’s case.
This type of situation is not unique to France, where it’s designed to retain employment: England and the USA have broadly analogous procedures to shield businesses from creditors to give time to recover, or be sold as a going concern without crippling liabilities.
While other boatbuilders have insisted on similar videos being taken down under threat of legal action, Grand Large Yachting didn’t take this approach. Following the video’s posting, co-founder Xavier Desmarest instead invited Lawson to Lorient to meet with him and ORC’s new marketing and communications director Pierre-Yves Poulain.
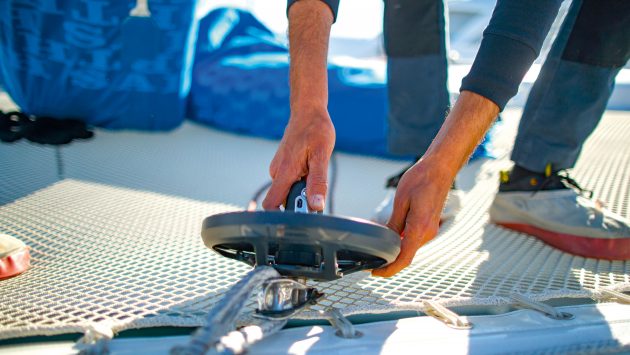
Installing equipment on a new yacht being commissioned at Grand Large Yachting. Photo: Robin Christol/Outremer
If Lawson opts to buy his boat back from the receiver, they have offered to repair it at cost, with him filming the process, even though it’s neither a boat they built nor one for which they have a legal responsibility. “They have enough pride in their workforce, their processes and the quality control they’ve introduced, that they’re standing up [saying], ‘we’ve nothing to hide, film it – we’re proud of our story’.” Lawson told me.
“I think that’s brave. And it’s a 180° turnaround on the previous owner who always was flanked with lawyers.”
In the months since buying the ORC assets and brand, Grand Large has invested considerably in transferring Outremer’s expertise to the Lorient site, including quality control systems and scaling up output to a more industrial, rather than artisanal, scale. With Outremer 45 production having moved to Lorient, the workforce there has increased from 60 to 100 people and I’m told Outremer’s industrial director is currently spending four days a week on site.
Pre-handover inspections
Even if it’s not possible to appoint a surveyor to monitor the build of a boat, would engaging one to inspect the vessel before handover be helpful? When I asked Lawson whether this might have identified all the problems with his boat he was initially sceptical, saying that while it should have unearthed some defects, others were unlikely to have been spotted – though this was before NDT testing using ultrasound became as commonplace as it is today.
Even that may not be easy to implement before handover of a new yacht. It’s perhaps not a surprise that dealers are not keen on the idea of a pre-handover survey and instead reassure buyers of the comprehensiveness of their pre-delivery checks, the effectiveness of the builder’s warranty, and the processes they have in place for snagging.
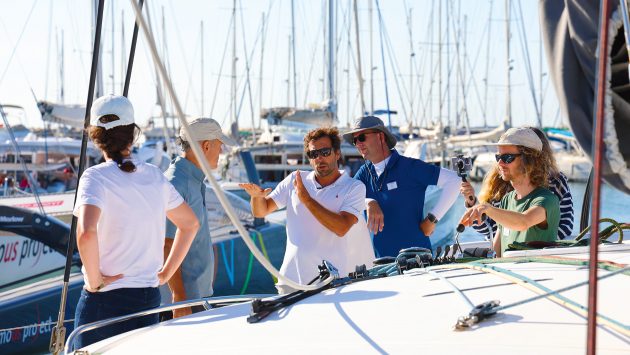
Outremer runs regular practical training courses to help familiarise owners with their new yachts. Photo: Robin Christol/Outremer
UK-based surveyor Nick Vass, for instance, tells me he generally only becomes involved once the relationship between buyer and dealer has already started to break down.
He has dealt with problems such as bubbling antifoul as a result of improper surface preparation and priming, deck fittings lacking effective sealant, but also others with serious safety issues, including one two-year-old yacht with corrosion of saildrive and hull anode bolts caused by stray electrical currents that had potential to sink the vessel.
Surveyors are not structural engineers, so can only tell you whether a boat appears to have been built according to expectations. Notified bodies are responsible for ensuring legal standards defined by the Recreational Craft Directive are met. However, Lawson is critical of this process, which others in the industry have described as ‘leaving holes in the safety net’.”
Despite a tightening of the regulations six years ago, manufacturers of yachts with a hull length under 12m need only an independent stability and buoyancy assessment. It’s only larger craft that need a notified body to approve design and engineering calculations, but production boatbuilders can still self-certify they have built each boat to that design. And their quality control procedures are not subject to scrutiny.
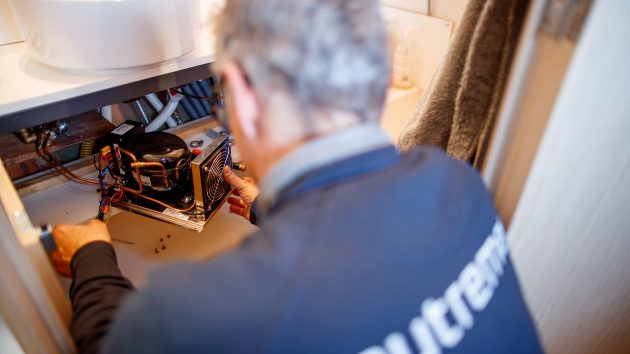
Staying near to the yard or dealer for a good period to iron out any problems is prudent. Photo: Robin Christol/Outremer
There’s therefore a risk that genuine mistakes can pass through without being picked up. Lawson also points out that this system, “means that cowboy builders can exist in the same space as reputable, decent companies.”
Questions to ask
Fortunately, however, the overwhelming majority of boat buyers appear to be happy with their yachts. The level of repeat business achieved by many well established yards is testament to this and plenty of recent used yachts survey well when they change hands.
But to avoid surprises at a later stage, in the early steps of negotiating to buy any new boat it’s worth establishing who will be responsible for snagging and whether they’ll travel to the boat, or if you’ll be expected to take the boat to them.
This is particularly important for those intending to sail long distances, who may need to plan more local sailing before crossing an ocean. On the other hand, many dealers are able to offer attractive packages for berthing, at least for the first season after handover, which means it’s effectively on site for any remedial work.
Beyond that, in the absence of greater oversight in the industry, maybe the best solution is simply not to overextend finances when buying a new boat. Experienced owners of second-hand craft know it’s important to make provision for unexpected expenses and the same may be true when buying new – so don’t get talked into buying a bigger boat than you really want, however good the deal appears to be.
If you enjoyed this….
Yachting World is the world’s leading magazine for bluewater cruisers and offshore sailors. Every month we have inspirational adventures and practical features to help you realise your sailing dreams.Build your knowledge with a subscription delivered to your door. See our latest offers and save at least 30% off the cover price.