The LA 28 is a beautiful, cold-moulded wooden trailer-sailer that was designed to be unique, and has now sold nine boats across Europe. Sam Fortescue steps on board
Appropriately, it’s a long train ride through thick, thick forest before I reach the LA Yachts yard on the banks of Lake Müritz in central Germany. This seems apposite because the boat I’ve come to see is an exquisite example of how wood is just as relevant as ever when it comes to boatbuilding.
In truth, the LA 28 has little in common with the endless rows of fir that fringe the lake; she is cold-moulded from nobler stuff. But it is striking that this young shipyard chose to build in wood. I ask yard owner Lothar Fichtner why.
“It’s lighter than GRP and cheaper than carbon,” he says without blinking. So much for the romance of traditional construction, then. In fact, there’s little about this vessel the boatbuilders of 100 years ago would recognise.
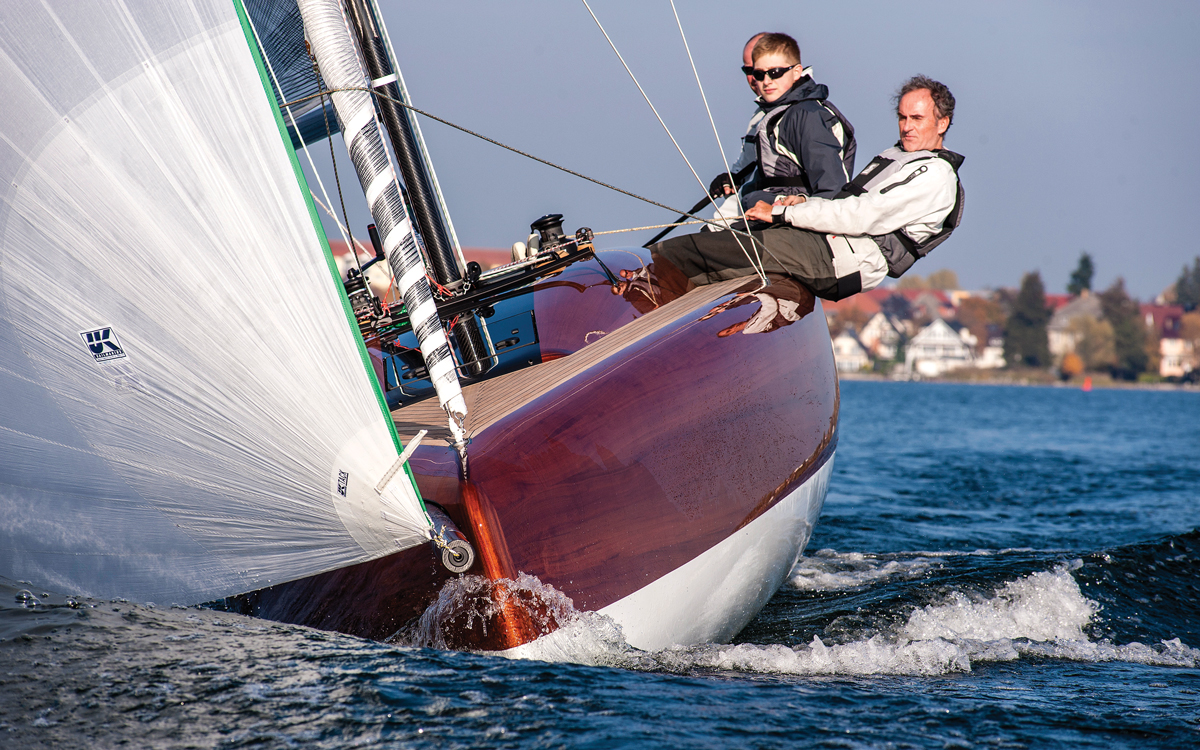
Around 60kg of Sicomin epoxy is used in the lay-up. Photo: Soenke Hucho
For one, cold moulding is a technique that relies heavily on epoxy resin to stick each layer of wood to the last and sheath the whole structure to keep the water out. Then there can be as much or as little carbon in the rig and the finish as you want, while propulsion comes courtesy of a Torqeedo electric motor.
Despite her elegant tumblehome and the plunging curve of her coachroof, this is a thoroughly modern boat. “The best of modern and traditional,” Fichtner says.
The story of the LA 28 begins with the desire of a wealthy man to have a beautiful sailing toy. Lothar Fichtner was that man and, having sold his engineering business, he wanted to enjoy more of life from his second home on Mallorca.
Article continues below…
Revolver: Bruce Ritchie’s gentleman’s racer blends traditional and modern craftsmanship
“I wasn’t expecting this,” said Michael Ritchie when his 83-year-old father Bruce showed him the lines he had drawn up…
European Yacht of the Year 2019: Special yachts
This category assembles a varying mix of interesting craft, many of which we might otherwise not have had the chance…
He approached a boatbuilder in the Muritz region called Andreas Zehle who specialised in the building of the German 20er Jollenkreuzer racing dinghy class, also cold moulded. Then he drafted in designer Martin Menzner from Berckemeyer Yacht Design in Laboe on the Kieler Fjord.
This small design house has worked on everything from dinghies to high-latitude yachts, using a range of construction materials and techniques. Crucially, Berckemeyer is strong in cold-moulded yacht design, or ‘speed strip’ as they call it.
The brief was for a trailerable 8-9m boat, that was “simple to rig, as single-handed as possible and with excellent sailing characteristics,” Fichtner explains. “I am bothered by the current development in boatbuilding. Almost all boats look the same. I wanted something exclusive that is modern in design and traditionally built.”
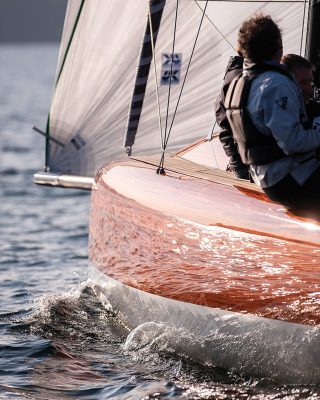
It takes more than 15 coats of varnish to achieve this degree of shine on the finish. Photo: Soenke Hucho
Menzner is a successful J/80 sailor himself, and the two men quickly saw eye-to-eye. The whole design process took just three months. Fichtner had no clear idea of it at the time, but he wasn’t just buying a boat, he was establishing a yard.
“I founded the shipyard because two boatbuilders were unemployed and I wanted to have a boat for my area in Germany and Mallorca,” he recalls. But one thing led to another, and Fichtner is a naturally ambitious man.
“We had a lot of success at trade fairs and continuous orders. Then I found my way into Germany’s Yacht magazine.” They have now sold nine boats since 2015, when the first garnered rave reviews at Interboat in Friedrichshafen.
Working with wood
Cold moulding requires a rough plug to be made, but no female tooling is needed, making it much cheaper to set-up than in the case of GRP or carbon. The plug around which the hull is formed is simply made from strips of softwood fastened around CNC-milled frames. It’s quick, cheap and relatively easy. The natural flexibility of the 2.5mm strips of wood used in cold moulding the hull iron out any imperfections in the mould.
The first stage of the process is to place a layer of plastic sheeting over the mould. Then the strips are bent into shape and clamped in place to hold their form. Each layer is bagged and vacuum infused with Sicomin epoxy resin, which soaks into the very top layer of the wood and helps to bond each strip edge-to-edge.
Each layer is laid in a different direction to the previous: longitudinal strips of okoume first, then lateral, then diagonal. For the outer layers, Lothar prefers African mahogany (khaya), giving a warm, reddish finish to the hull, which is many times stronger than the equivalent in glassfibre, and lighter too.
The deep curve of the tumblehome is all part of the hull shape, so it isn’t possible to mould the whole hull at the same time. Instead, there are two symmetrical plugs, one for the port side, one for starboard.
When the two halves are finished, they are simply epoxied together in the middle with a sort of low keelson covering the whole length of the joint for extra strength.
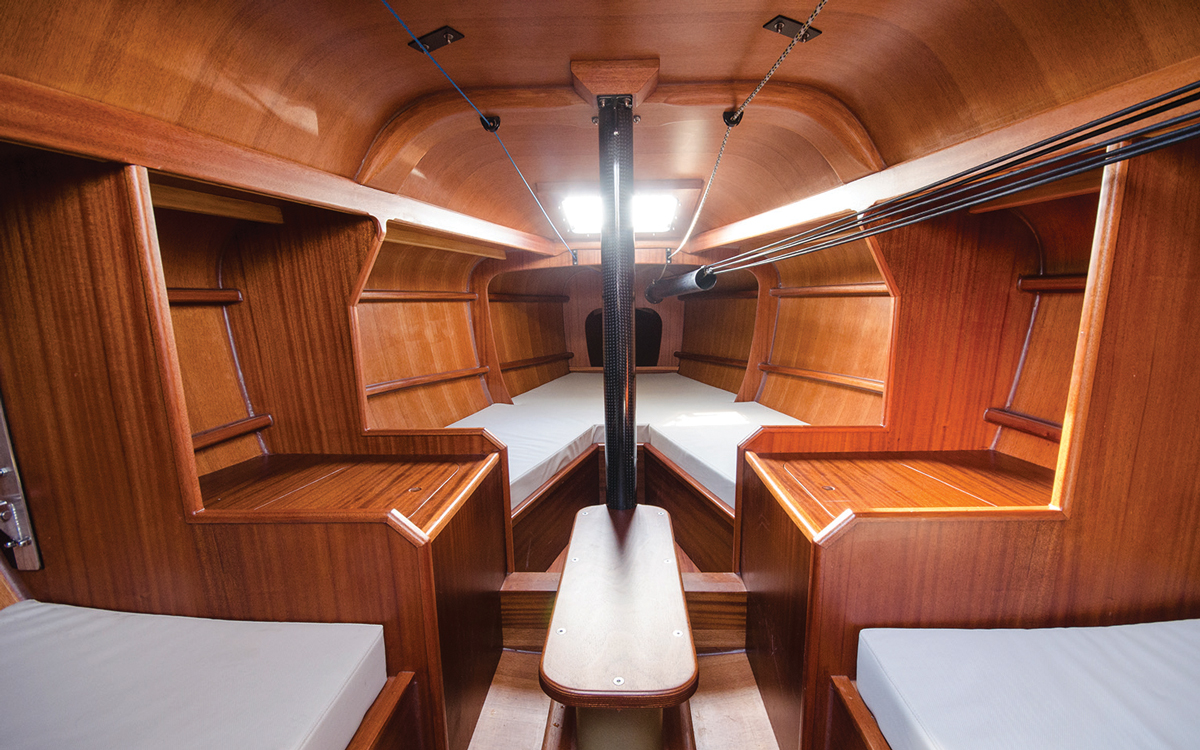
Cold moulding leads to a beautiful interior finish. Photo: Soenke Hucho
At this stage, the hull is still just a hollow form, albeit a beautiful one. Extra strength must be added next, which is achieved by ‘backfilling’ frames, ringframes and stringers – all glued into place after the event. These support the stresses of the mast, the shrouds and the keel, and provide structure for the transom, keelbox and so on.
The finish is a matter of personal taste – every owner makes their own decisions on this. Some have opted for carbon detailing; a layer of carbon epoxied around the aluminium mast post, for instance, a carbon keelbox and carbon fibre pads where the line for the retractable bowsprit passes through the companionway bulkhead into the cockpit. The mast and boom are both in carbon, with sails recommended in X-Drive carbon from UK Sailmakers.
Others have requested a white painted interior (a lot more work, observes Fichtner), or different woods used in the construction process to give a slightly different finish. The point is that every boat is unique and can be formed and specified to fit its new owner’s wishes: engine or no engine; spade rudder or transom-mounted kick-up rudder.
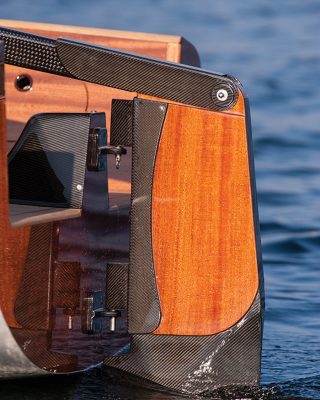
LA Yachts uses a very light wooden core for the tiller, then laminates it with carbon fibre. Photo: Soenke Hucho
Below the waterline the usual keel is a 600kg lead bulb, but again you can choose from a number of options. With the fixed keel there is the option of a 1.7m, 1.8m or 1.9m draught – depending on where you sail and how aggressively rigged she is.
But the hydraulic lift is proving a popular option, which reduces draught by 0.9m in the raised position. It’s a handy option for shallow waters, and makes it more feasible to land wherever the fancy takes you – perhaps with a family and a picnic basket.
True to the boat’s thoroughly modern character, Fichtner worked closely with Torqeedo in designing the LA 28 to use one of the company’s 2.5kW electric drives.
This is permanently mounted on a pod under the cockpit, but the throttle lives out of sight on a fold-down panel that pops out of one of the cave lockers. It’s a neat solution to the fact that the Torqeedo control is chunky and modern, and rather at odds with the otherworldly lines of the LA 28.
Controlled growth
The boat is resolutely designed to be simple to handle. “They sail easily and they’re very light. I can come into port by myself, and handle her myself,” Fichtner says. “With a bigger boat you always need a team – you are never alone.”
That said, there is a bigger boat on the horizon. Taking its cues from the look and handling of the LA 28, a larger 35-footer has been designed and will shortly enter the build phase. At 10.8m long, she can still be trailered, thanks to an all-up towing weight of just less than 3.5 tonnes.
“I want to invest in quality,” says Fichtner determinedly. “My dream would be to build just three boats per year.” There seems to be a preponderance of billionaires among the ownership ranks of LA Yachts, so perhaps three a year is more ambitious than it sounds.
Specification
LOA: 8.8m (28ft 11in)
LWL: 8.0m (26ft 3in)
Beam: 2.5m (8ft 2in)
Draught: 1.7-1.9m (5ft 7in-6ft 3in)
Keel raised: 0.8-1.0m (2ft 8in-3ft 3in)
Displacement: 1.5 tonnes
Ballast: 600kg (1,322lb)
Engine: Torqeedo Cruise 2.0FP
Price: €120,000 (ex. VAT)