Developments in the structure and treatment of glass, which is now tougher, stronger and more malleable, are having a major impact in superyacht design. Andi Robertson explains
It was once virtually a given that the bigger and more elaborate the superyacht, the more detached and cut off those on board were from the outdoors they had invested so much to enjoy.
But as glass design and engineering technology move forwards at a pace that is now driven primarily by building and automotive architecture, the superyacht design houses are increasingly able to redress this balance by designing in more glass.
With glass they can bring the outdoors indoors. Now superyacht guests can enjoy that remote atoll, the secluded, unspoiled anchorage, that unique all-round panorama for a stateroom dinner, the fiery sunset at sea, the moon rising overhead – all from the temperature-controlled confines of a sumptuous cabin.
“The whole reason that people buy boats is to get out on the water and to see and enjoy the water,” says designer Malcolm McKeon. “The use of glass gives people on board that connection to the water. The bigger the boat, the less the connection. So to get back the connection more and more glass is being used in hulls.”
Maximising light and space is only one feature that large areas of glass allow; it is the ability to deliver the ever-changing connection with the land and seascapes that is fundamental to what the modern superyacht designer can create.
“On Aquijo (86m/282ft) there is 270° viewing from all angles of the master stateroom,” declares Bill Tripp. “It’s about sitting there and thinking the view is the most beautiful ever. Until, of course you move on to the next place. But that is entirely dependent on glass and how you use it.”
Growing importance of glass
Glass is becoming more prevalent in design, but it has been hard to get classification societies to accept the growing importance and use of glass in a structural way as well as its aesthetic and practical role.
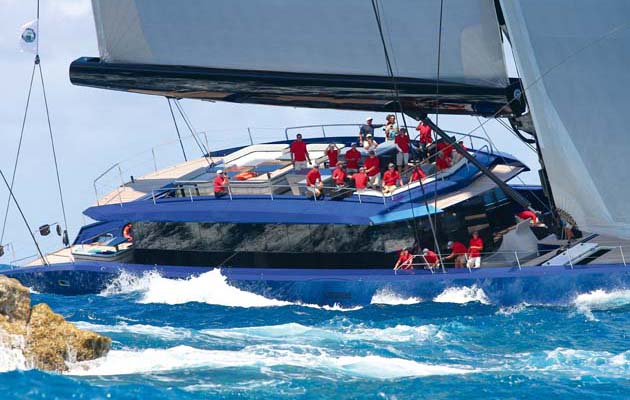
The Tripp-designed 50m/166ft Better Place ably demonstrates Wally’s concept of ‘inside-outside’ living, aided by acres of glass. Photo by Ingrid Abery.
McKeon, for one, has been commissioning finite element analysis to prove that glass can be used to a greater extent in more structural situations: “We still design with glass at 2.3 times the strength of the surrounding structure,” he explains. “The thickness depends on the curvature of the glass. For Ganesha (46m/151ft Vitters sloop) for example 5m x 1.5-2m glass panels were cold-bended to a certain degree. But if you want a lot of curvature you need to chemically toughen it in a bath (which is usually to a maximum of 5m).”
Philippe Briand is well known as an advocate for glass: “I am a fan of lots of glass. I feel we should be able to use more and more glass. I have always had a good relationship with the classification societies. They are changing now and we are finally allowed to use glass as a structural element.”
He adds: “I like to use glass with the minimum of constraints and am using it more and more. The 3D shapes we can make are improving all the time. Glass technology really is opening the design space more and more.”
Hull windows are becoming progressively larger as technology improves, not just in the glass itself, but the way the windows are set into the hull.
However, according to Briand, weight is still the enemy in hull forms of the modern performance superyacht: “More glass is more weight (in comparison with modern hull materials) and more weight is not good, and so we have to be strict about how we use it in the hulls.”
On some of his designs Briand has employed multilayer compound security glass into which is embedded multifunction sensor technology, which means any changes or threats are detected early and linked to the alarm system.
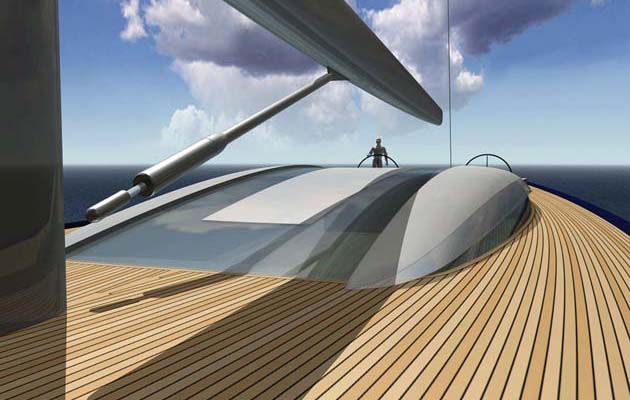
Philippe Briand is a keen advocate for the structural use of glass. In this 40m/130ft concept, he uses curved glass to great effect.
Jim Bolton of UK-based Trend Marine Glass explains: “Interlayer technology now allows us to take hull structure out, to come out unframed and replace it with stiff, strong glass panels, direct-bonded flush with the hull and these include flush-bonded opening windows.
“The classification societies have moved on significantly to accept unframed solutions. On the interior this has the advantage of a smaller, more compact window reveal.”
Bolton explains: “An interlayer is created by using a heat-sensitive adhesive – it is heated in a vacuum. The interlayer floats as a clear adhesive. The structure created using modern hydrophobic interlayers is a game changer.
“We are still extensively sag-bending, which gives a very clear, optically superior piece of glass. It can be bent in two planes so, for example, you can get a conical effect, or double curvatures. It is bent on articulated tooling and it is then chemically toughened rather than standard thermal toughening. It is laminated together because the break pattern is different, but it is a strong piece of glass, which can take more shape and the optical clarity is good.
“What is changing is the tooling, which allows us to make glass into much more extreme shapes. The technique of sag bending is evolving and that is in line with the abilities of 3D modelling. Glass manufacturing technology has had to catch up with the designers’ CAD drafting and five-axis production.”
Following the car industry
In some respects the use of glass in superyacht design and build has a crossover from the automotive industry. The glazed part of cars has increased in area by 15 per cent over the past ten years. Glass thickness has been reduced by ten per cent, but contributes to 30 per cent of a vehicle’s structural integrity.
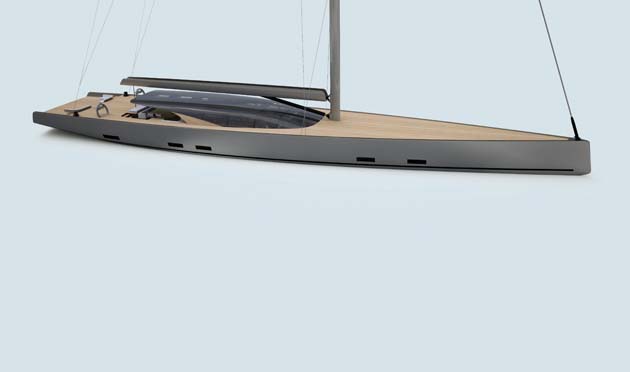
An innovative use of glass for the entire coachroof aboard Malcolm McKeon’s 51m/167ft design.
Corning’s Gorilla Glass is being used by some superyacht designers, but it is only available in limited dimensions. This super-durable glass is used on smartphones and tablets, and is already utilised on the BMW i8 hybrid sports car because it is lightweight and scratch-resistant.
Superyacht designers and engineers are excited by Gorilla Glass, but in comparison with the automotive industry superyachts are a mere brand showcase, a prestigious niche amid the potential 4.5 billion square metres that the market for automotive glass represents.
James O’Callaghan of Eckersley O’Callaghan, one of the world’s leading engineering design practices – widely renowned for the glass in Apple buildings such as the 5th Avenue Apple store in New York and the Embassy Gardens Sky Pool in London – has been helping superyacht designers push the glass design and engineering frontiers since the company was invited to contribute to the innovative glazing design solutions for MY Venus six years ago.
“Until that point our work in glass, in particular structural glass, had been limited to architecture,” says O’Callaghan. “The striking thing when comparing the two industries at the time was the distinct lack of understanding the luxury yacht market had of the potential of glass use. We found it relatively straightforward to introduce the shipyards and naval architects to ways in which they might open up the opportunities of glass use by illustrating to them the advances in fabrication and design that had been occurring in the building industry.”
He remembers it as a turning point: “We feel that designers have responded with more ambitious designs, including challenging glass ideas. This is also heavily influenced by owner trends for more light and transparency in the yacht designs they prefer.
“Technically weight always plays an important part in yacht design, perhaps more so on the high-performance sailing yachts we have been involved with. Therefore, ways in which you can optimise glass thickness are as important to the equation as the manner in which you can fill large open apertures with frameless glass solutions.”
Larger areas of glass are now used with much less structure around to support them. This usually means engineers are required to specify heavier, thicker glass, but this is offset in part by the reduction in framing structure along with the obvious, desired benefit of openness. The glass industry has been revolutionised over ten years to produce glass with a maximum dimension of 15m, where ten years ago that maximum was six metres.
O’Callaghan concurs: “That is a remarkable evolution for an industry that is typically slow in developing. It’s an exciting time to be involved with the material and how it can be used in yacht design. In some ways it reminds me of the introduction of composites into yacht design and opportunities that material afforded the designers in performance and form.”
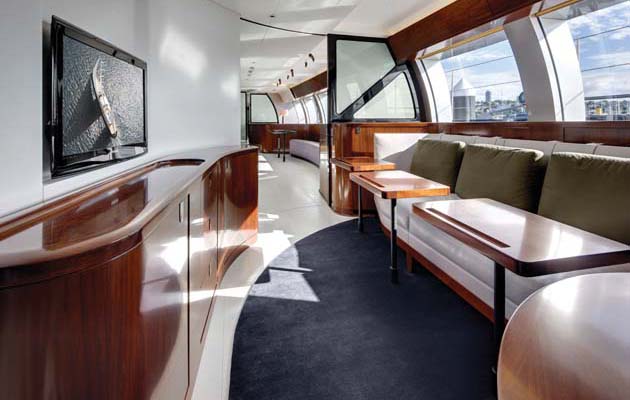
Clear inside and out – from the decksaloon aboard the Briand/Alloy Yachts 67m/220ft Vertigo guests get a terrific view.
Gorilla Glass
Gorilla Glass is made using a chemical strengthening process. Glass is placed in a hot bath of molten salt at 400°C. Larger potassium ions from the salt bath replace the smaller sodium ions. The process allows the potassium ions to diffuse deeper into the glass, establishing a high compressive stress inside.
James O’Callaghan uses the new families of thin glasses to great effect: “Gorilla Glass is a fantastic new development in glass. It forms part of a family we now refer to as ‘Thin Glasses’, which really mean high-strength glass sub 2mm in thickness. The additional strength over regular glass is significant and means we can leverage this strength specifically when needed – for example, in high impact loading conditions, without necessarily increasing the glass thickness (and therefore weight) to resist loads that rarely, if ever, occur.
“As far as classification is concerned, I think the issues are the same irrespective of the specific material. There needs to be more education such that they better understand what the glass can do. We need to collate a series of tests, along with supporting analytical data, to show how all glass can be used safely and efficiently before we can expect the class and rules officials to accept it. It is on the shipyards and class officials to instigate this through the most effective channels they can so that we can reach a level of comfort in the use of glass going forward in these more specialist applications.”
Bill Tripp also likes Gorilla Glass because it is lighter, but feels that the regulatory bodies are erring on the conservative side in their consideration of new glass technology.
“It is a regulatory hurdle. It seems as if barriers are in our way and we are having to push them. We had it years ago with carbon, but first and foremost we want to be able to design and build seamlessly with the best materials. But the reality is different. The technology should be readily available. Chemically strengthened laminates are from technology starting 25 years ago.”
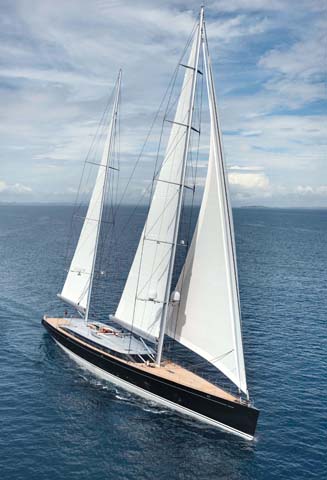
Vertigo.
Layers and treatments
Treatments to glass are exciting and innovative, bringing practical and economic benefits as well as simply enhancing form and function. Reflective layers can reduce heat and UV transfer by half. These modern heat-reflecting glasses mean a significant reduction in the air conditioning requirement, so designers can specify smaller, lighter units in new superyachts.
Electrochromics mean colours in the ‘smart glass’ can be changed to control the light and heat that passes through the windows, and electrochromatic windows can switch between being translucent and opaque. Applications such as this are reducing the use of curtains and blinds where privacy is required.
On the horizon perhaps are new microtreatments to the surface of glass, which can make it much stronger. Researchers at McGill University in Canada have taken the tiny interlocking patterns from the structure of sea shells and engraved them into the surface of glass, creating networks of tiny micro cracks. The glass becomes more formable and less brittle and is 200 times stronger than conventional glass.
Glass is in the midst of a technological revolution precipitated by industries sharing the same desires and
vision – superyachts are just one high-profile area where the benefits are clear.