Toby Hodges and Rupert Holmes take a look at some of the latest eco-friendly sails technology, from recycleable to recycled materials
Sails are predominantly made from new plastics, chemicals and virgin fibres, but some latest developments may help address that and make eco-friendly sails a real option when you buy your next set.
As consumers, looking after your sails and making them last remains key. But for manufacturers, developing circular economy products should be the holy grail – using sustainably sourced products which can be recycled again to make raw materials. While Dacron, Dyneema, carbon fibre, aramid, Mylar films, chemicals and glues remain the mainstay of sailmaking, that seems a pipe dream. However, we understand, for example, that North Sails has a team working on circular cradle-to-grave recycling for the polyester versions of its 3Di sails that would enable the company to derive raw materials for new fabric from end-of-life sails.
Meanwhile, a couple of large lofts have forged ahead with looking for solutions for high standard laminate sails using greener tech. OneSails is producing sails which can be broken down for recycling after use, while Elvstrom has launched its EKKO range of laminate sails that are made entirely out of recycled materials.
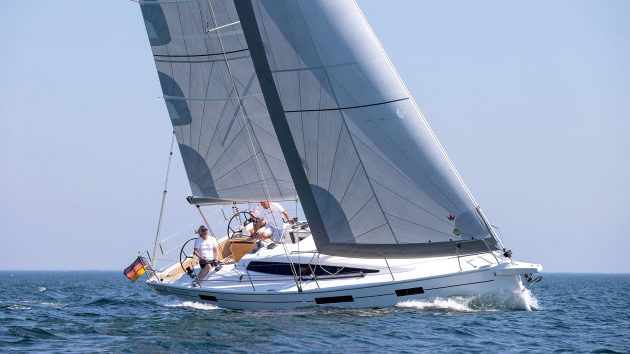
eXRP EKKO mix of black polyester fibres with white taffeta produces a grey sail
Elvstrom eXRP EKKO – Sails from plastic bottles
eXRP Cruise is the latest addition to Danish sailmaker, Elvstrom’s more sustainable EKKO line, sails made from recycled plastic bottles. Essentially, this is a high end laminate, where the main constituents are all made from recycled PET/polyester – including the UV film, the taffeta and fibres.
We got to see the product in use in La Rochelle, trialling it on a new Dufour 470. The European Yacht of the Year jury was impressed enough with seeing the performance, and with finding out the lengths to which Elvstrom has gone to implement its construction, that we gave eXRP EKKO a special mention award.
Three different weights are offered: light, medium and heavy. To get stability in the heaviest version (the eXRP Cruise laminate we sailed with) Elvstrom had to add some UPE virgin fibres – “but only a few grams per m2 to get it up to a 50ft boat,” reasoned Flemming Christensen, product development manager and the driving force behind the new greener sails.
Article continues below
The grave human cost of teak wood – and alternatives
Teak is synonymous with boatbuilding. But the Environmental Investigation Agency recently issued a report on an 18-month investigation into the…
Avvento: The all-electric Spirit 44e that’s pushing boundaries
Boats have been built of wood since Noah first put axe to tree. For devotees of the classic style, Spirit…
Teak alternatives: 4 options for decking that doesn’t cost the earth
Everyone loves an immaculate teak deck. They look great at boat shows and at chic Mediterranean quays, as well as…
Elvstrom’s tests have shown eXRP to be highly form stable, even more stable than similar laminate from market competitors, thinks Christensen: “with no real optical difference to other laminates made from virgin materials”. The EKKO option is available on Elvstrom’s performance and bluewater cruising and club racing products.
“The goal was to make as green a construction as we could,” Christensen told me while trimming the stackpack mainsail. He explained how laminate sails use a chemical on the outer layer of taffeta as a UV inhibitor. Elvstrom managed to avoid this by using a UV PET film within the sail, “which gives us a bit more protection to the polyester fibres inside”. The PU glue also has a UV inhibitor in it which helps promote longevity.
Christensen thinks using recycled content rather than focussing on trying to develop recyclable sails is the way to go for now.
“There is no product on the market that can be fully recycled because they all have glue inside. So our goal was to make a new product from scrap material,” he said.
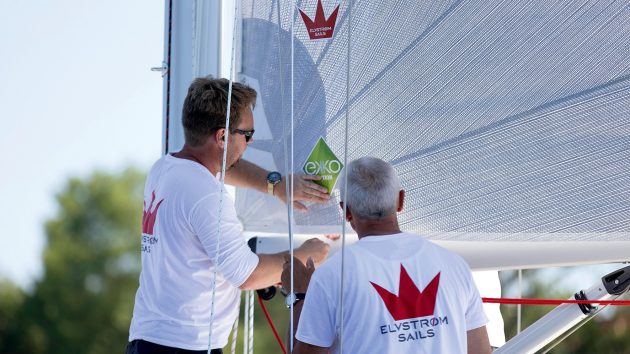
Falling costs of recycled materials mean EKKO sails are competitively priced
Why only now?
Laminate sails largely comprise polyester products such as Dacron and Mylar, so why has it taken this long for a loft to start producing sails made from recycled products? Firstly there’s the issue of sourcing recycled materials that are a reliably high standard.
Elvstrom ended up teaming up with cloth manufacturer Challenge but first needed to establish reliable suppliers of recycled polyester. “When you recycle polyester, you have to find the right quality,” said Christensen. “It took some time, but we found some in Holland and then in China.”
He also points out that it’s to do with the demand:cost spiral. Where just three years ago it cost 10-15% more for the raw materials, such is the demand from the textile industry today that the price of recycled PET has come right down.
The result is that there is little difference in pricing, whether you choose the EKKO product or not. “We hope that the fact you do not really have to consider the price issue on this one, will make the decision to go for the more sustainable version very easy,” Christensen reasoned. “We believe we can make something equivalent to a high quality virgin fibre sail today.”
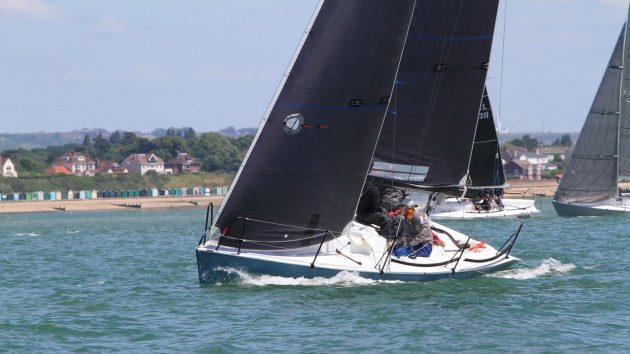
OneSails 4T Forte sails can be broken down for recycling after use
OneSails 4T Forte – Sails you can recycle
Unfortunately there’s no way to recycle a sail that’s made out of a mix of material such as carbon, aramid, Mylar and glues. However, in 2013 Piercarlo Molta, OneSails’ R&D coordinator and CEO of Flexon Composites, producer of 4T Forte sails, set out to develop a new material that can be recycled, without compromising shape retention, longevity and reliability.
“At that time I decided to get rid of carbon and Mylar and move towards materials and processes that would be more sustainable,” he told us, “but we still had to ensure the performance would be the same.”
Conceptually the general idea is straightforward: to build the structure of the sail using a single material, plus a layer of thermoplastic melting matrix in the sandwich. These are vacuum bagged and then heated over a shaped air suspension surface, so that when the thermoplastic melts it flows through all the other layers, bonding all the elements together in exactly the right shape.
At the end of its life the sail can be recycled locally in a standard industrial recycling plant. The first stage is to mill it into small pieces, heat to extract the thermoplastic, then heat further until the fabric is molten and can be extruded into pellets. As an example, one of the sails Pip Hare used in the Vendée Globe has already been recycled in this way.
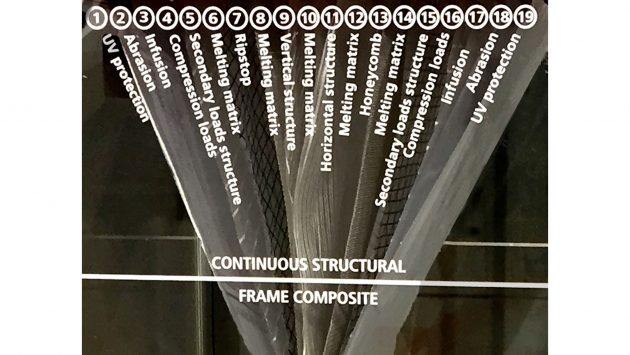
4T Forte sail fabric is constructed from multiple micro-layers
On the downside, you can’t get back to a pure polyethylene, so this is not a full circular economy model in which old sails provide the raw materials for new ones. However, the pellets can be used to create a variety of other new injection moulded products.
The engineering involved in creating such a sail is not simple. The fabric is a composite made of 16-20 micro layers, all of which are fine tuned for each sail and each boat. In addition to the structural fibres and thermoplastic melting matrix, they include a secondary grid for support and stability, a honeycomb that increases stiffness while keeping weight as low as possible, plus UV and abrasion resistant outer layers.
Other than the thermoplastic matrix, the base material for every layer is pure high modulus polyethylene (UHMWPE), a part of the same chemical family as Dyneema. This has a very similar modulus to carbon, but crucially enables the sail to be constructed from a single material – a prerequisite for recycling.
Molta is keen to point out that the thermoplastic film used is not a conventional glue. Its chemical properties are not changed at any stage of the process, which means it can be recovered entirely by heating.
In addition to producing sails for racing and cruising yachts of all sizes, he’s “very involved” in emerging technologies for wind powered shipping, developing sails for vessels with a total sail area of around 4,000m2 and individual sails of around 600-700m2 each. To give a sense of scale, a 4T Forte mainsail for the ClubSwan 125 Skorpios is around half that size at 380m2.
If you enjoyed this….
Yachting World is the world’s leading magazine for bluewater cruisers and offshore sailors. Every month we have inspirational adventures and practical features to help you realise your sailing dreams.Build your knowledge with a subscription delivered to your door. See our latest offers and save at least 30% off the cover price.